Articles | Technical
Fire resistance test procedure and plasterboard’s performance
Monday, 11 December 2023
By Frank Kang
Gypsum plasterboard has served as a construction material for many decades, finding widespread use in both residential and commercial buildings for interior linings. The manufacturing process involves heating finely ground gypsum to approximately 140°C, driving out moisture to lose about 75% of its water of crystallisation. This produces dehydrated calcined gypsum powder, calcium sulphate hemihydrate which is also known as Plaster of Paris. Gypsum plasterboard is then manufactured by mixing the Plaster of Paris with water and various raw materials, and letting the slurry harden between two sheets of cardboard-like plaster liner board.
In the event of a fire, gypsum plasterboard undergoes a dehydration reaction as bound crystalline moisture evaporates. This causes gypsum to lose strength and eventually decompose into a powdery state again. This decomposition reaction is endothermic, and hence, excellent fire resistance can be achieved. The performance of the plasterboard depends on composition of the plaster, thickness, density, and the number of layers.
In New Zealand, fire-resistance testing is commonly conducted in accordance with AS 1530.4:2014, evaluating the behaviour of vertical or horizontal construction elements exposed to fire conditions. The first step is to construct the test specimen in a specimen holder and then mount the holder into the fire furnace. The fire-resistance test is considered to have begun as soon as the burners are lit. The test specification generally follows the ISO 834 standard fire curve.
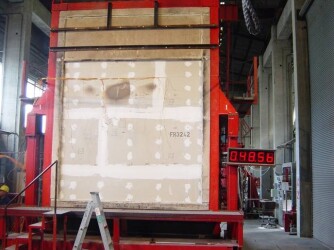
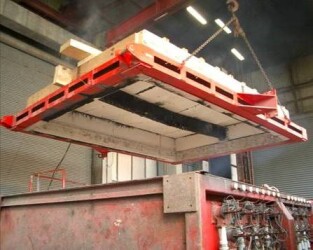
Full-scale fire-resistance test furnace for vertical (left) and horizontal (right) specimens.
The performance of the test specimen is assessed against three failure criteria: structural adequacy (failure to resist applied gravity loads during a fire), integrity (passage of flame or hot gases), and insulation (unacceptable unexposed face temperature rise).
The integrity failure is measured by cotton pad, gap gauges or sustained flaming through the test specimen. The insulation failure is measured as an average temperature rise of 140 degrees C, or a rise of 180 degrees C at any single point on the unexposed face of the test specimen. For loadbearing specimens, the structural adequacy failure is deemed to have occurred upon collapse, or when the following occurs:
In our fire resistance tests, we always install additional thermocouples within the test specimen cavity to collect temperature measurements at various cavity locations, framing members, and between layers. Although the AS1530.4:2014 test standard does not mandate these temperature measurements, except for the Resistance to Incipient Spread of Fire which is applied as a performance criterion in Australia but not in New Zealand, these additional data points help us to analyse what is happening within the cavity, build an in-depth understanding of our products and systems, and assist customers with engineering assessments and judgments.
Looking ahead, our technical team is in the process of revising the current ‘GIB® Fire Rated Systems, 2018’ and ‘GIB Noise Control® Systems, 2017’ literature, with a targeted release of the middle of next year. The updated literature will be a core resource for the accurate design and detailing of our performance systems.
Call the GIB® Helpline on 0800 100 442 for any assistance.
Read next
Articles | GIB Community
Bowled over: Former architect and lawn bowler joins Winstone Wallboards' Technical Support team
Monday, 11 December 2023 By Siobhan Page